Azazello
habitué
- Messages
- 1,109
- Location
- Italy
As you may have read on my restoration thread, my 334-10 gearbox (4 speed, old type pre-73) is missing 4th gear: even operating from the shaft out of the gearbox I can't find it.
Today I took the gearbox off the car in order to open it and check what's wrong, and hopefully have a light overhaul (mainly changing gaskets, because oring and oilseals for differential and main shaft have already been changed a few months ago when I first coupled engine amd gearbox).
I fear doing some damage just unscrewing bolts casually: anyone of you experts can give me some advice on how to open safely the gearbox in halves and what to check for in order to solve my problem?
Here it is a drawing of the kind of gearbox I am talking about.
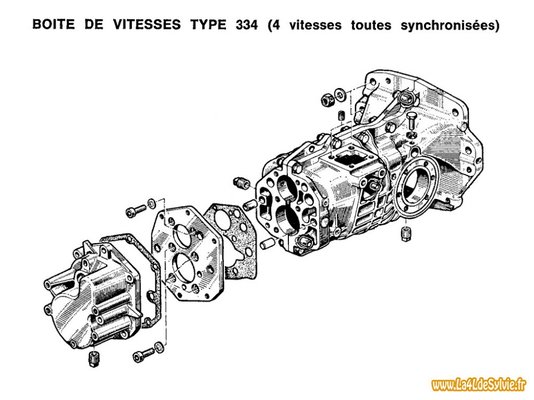
Today I took the gearbox off the car in order to open it and check what's wrong, and hopefully have a light overhaul (mainly changing gaskets, because oring and oilseals for differential and main shaft have already been changed a few months ago when I first coupled engine amd gearbox).
I fear doing some damage just unscrewing bolts casually: anyone of you experts can give me some advice on how to open safely the gearbox in halves and what to check for in order to solve my problem?
Here it is a drawing of the kind of gearbox I am talking about.
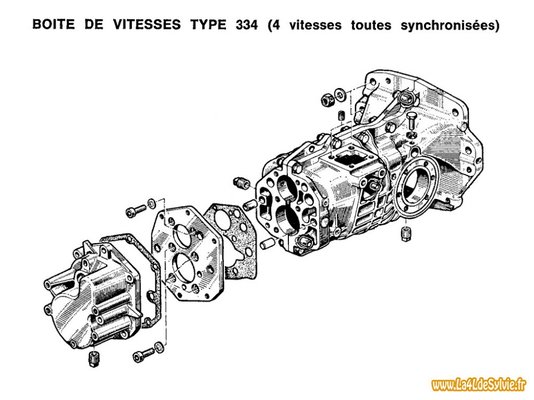