Homegrown
Enthusiast
- Messages
- 288
- Location
- Sweden
Prepare cylinders today.
Honing cylinders to get rid of glazing and get a good crosspattern for rings to bed in, try to take as little as possible. Low rotation speed and quick movement up/down. Use diesel with some oil in the cylinders and add WD40 in the process, very happy with the result.
After bores locks nice, I clean them thoroughly and start adjust cylinders to deck height. Hade to move around the shims some before to get what I wanted. I measured shims again today they were 0.10 0.12 0.15 0.16 I shimmed cylinder to tolerance with priority that cylinder pair standing against each other are absolute level.
When cylinder preparation where ready I check ring gap in respective cylinder and all was enough so I don't need to adjust. Rings from GOETHE looks the part.
Hurry to work
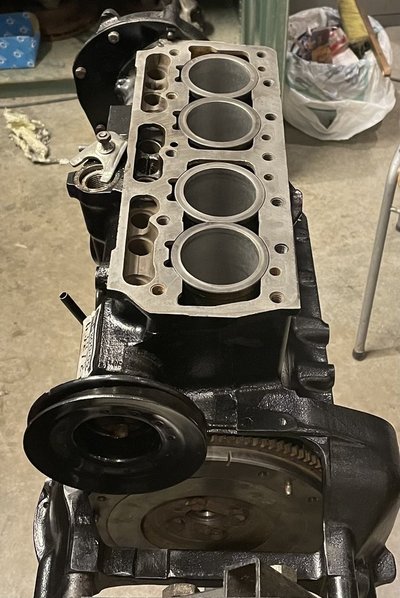
Honing cylinders to get rid of glazing and get a good crosspattern for rings to bed in, try to take as little as possible. Low rotation speed and quick movement up/down. Use diesel with some oil in the cylinders and add WD40 in the process, very happy with the result.
After bores locks nice, I clean them thoroughly and start adjust cylinders to deck height. Hade to move around the shims some before to get what I wanted. I measured shims again today they were 0.10 0.12 0.15 0.16 I shimmed cylinder to tolerance with priority that cylinder pair standing against each other are absolute level.
When cylinder preparation where ready I check ring gap in respective cylinder and all was enough so I don't need to adjust. Rings from GOETHE looks the part.
Hurry to work
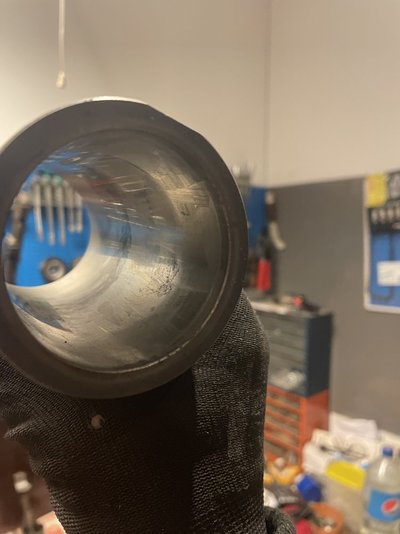
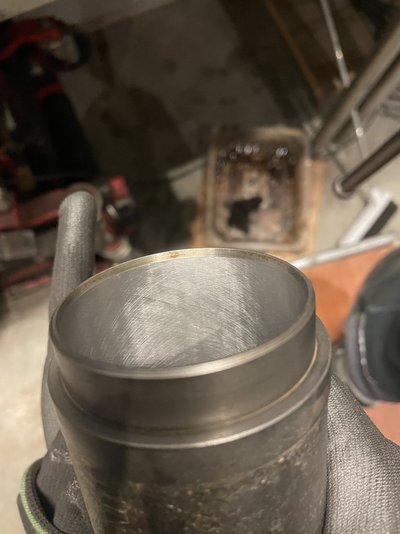
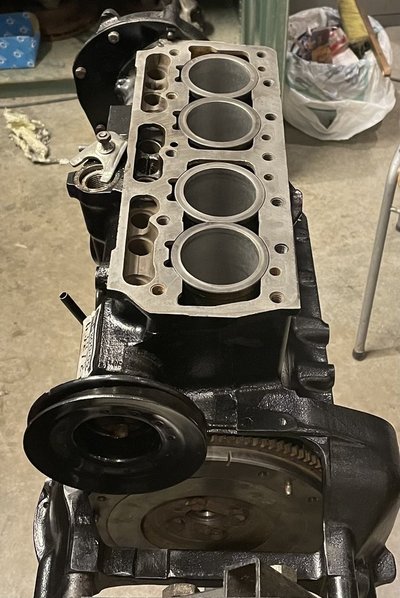